Classification
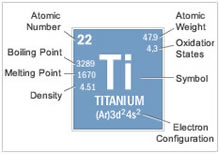
The factors affecting the super-plastic forming of titanium alloy
Submitted by admin on 11/04/2014
The influence factors of super plastic forming: the organization state of raw materials, grain size, and thickness uniformity, forming temperature, forming pressure and deformation velocity and other parameters.
1. The selection of the raw materials
The organization state and the grain size of titanium slab used for forming have a direct relationship with its super-plastic index. The plastic of big grain is very low, so it isn't suitable for the air pressure forming. Generally, the titanium alloy slab require the equated fine grain microstructure (grain size < 10 μm).
So the industry supply state TC3, TC4 sheet basically can meet the use requirements. But we must carry on the metallographic test and high temperature tension test on raw materials, after the confirmation of compliance with the requirements, we can begin to use it.
The thickness tolerance of titanium plate supplied by industry is large. The plate thickness uniformity requirements error can't more than ± 0.05mm. What's more, the local defects in thin and inclusions, segregation must be forbidden.
2. The forming temperature
According to the high temperature tensile data of materials, to select the appropriate temperature range, and we should also consider the die material temperature with the long-term use, convenient operation, prevent pollution and other factors, and then we can determine the reasonable forming temperature. From the view of engineering application, try to choose a lower temperature is more reasonable. This will prolong the service life of the die and improve the production efficiency, and it is convenient for operation.
3. The forming pressure and deformation velocity
In the process of titanium alloy pressure molding, the gas pressure is an important parameter for ensuring post mold parts. According to the shape and size of parts, the original thickness of the slab and the flow stress calculation, we can get a reference value.
The deformation velocity is a parameter which has a direct relationship with the forming pressure, from "α=Ke", we can see that the flow stress has a directly proportional relationship with "e". In order to ensure the flow stress in the process of forming stress is always in a small range, we must control the speed of deformation in the lower range. Generally the strain rate e < 10^ (-4) - 10^ (-1) seconds is appropriate. In the process of molding the general use of gas pressure control unit time increase the way to control the forming velocity. Such as forming in titanium ball bottom, in the first stage of R800mm forming pressure ball in 0.005 - 0.01MPa, in the second stage to step down to take 0.02 0.03MPa order R5 arc forming. We can assume that the deformation is more uniform, the deformation speed should be in the range of e < 10^ (-4) - 10^ (-1) seconds.
From the point view of engineering application, the deformation velocity can't choose too low, as long as we can meet the forming quality of parts, the forming speed should be as large as possible. This can help to increase the production efficiency.
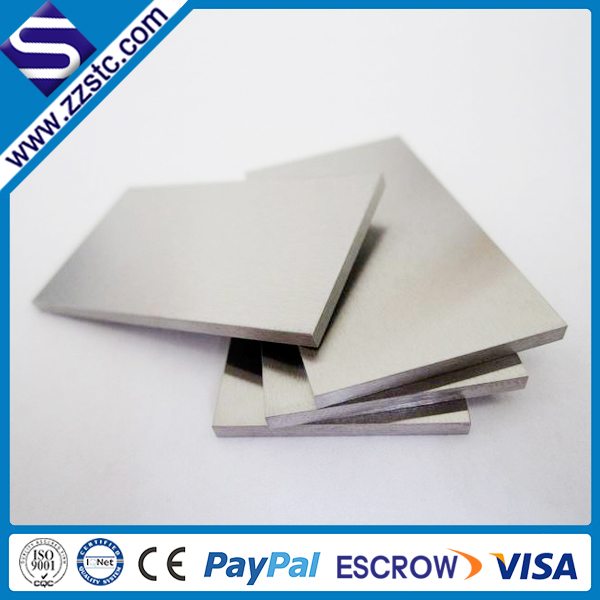
1. The selection of the raw materials
The organization state and the grain size of titanium slab used for forming have a direct relationship with its super-plastic index. The plastic of big grain is very low, so it isn't suitable for the air pressure forming. Generally, the titanium alloy slab require the equated fine grain microstructure (grain size < 10 μm).
So the industry supply state TC3, TC4 sheet basically can meet the use requirements. But we must carry on the metallographic test and high temperature tension test on raw materials, after the confirmation of compliance with the requirements, we can begin to use it.
The thickness tolerance of titanium plate supplied by industry is large. The plate thickness uniformity requirements error can't more than ± 0.05mm. What's more, the local defects in thin and inclusions, segregation must be forbidden.
2. The forming temperature
According to the high temperature tensile data of materials, to select the appropriate temperature range, and we should also consider the die material temperature with the long-term use, convenient operation, prevent pollution and other factors, and then we can determine the reasonable forming temperature. From the view of engineering application, try to choose a lower temperature is more reasonable. This will prolong the service life of the die and improve the production efficiency, and it is convenient for operation.
3. The forming pressure and deformation velocity
In the process of titanium alloy pressure molding, the gas pressure is an important parameter for ensuring post mold parts. According to the shape and size of parts, the original thickness of the slab and the flow stress calculation, we can get a reference value.
The deformation velocity is a parameter which has a direct relationship with the forming pressure, from "α=Ke", we can see that the flow stress has a directly proportional relationship with "e". In order to ensure the flow stress in the process of forming stress is always in a small range, we must control the speed of deformation in the lower range. Generally the strain rate e < 10^ (-4) - 10^ (-1) seconds is appropriate. In the process of molding the general use of gas pressure control unit time increase the way to control the forming velocity. Such as forming in titanium ball bottom, in the first stage of R800mm forming pressure ball in 0.005 - 0.01MPa, in the second stage to step down to take 0.02 0.03MPa order R5 arc forming. We can assume that the deformation is more uniform, the deformation speed should be in the range of e < 10^ (-4) - 10^ (-1) seconds.
From the point view of engineering application, the deformation velocity can't choose too low, as long as we can meet the forming quality of parts, the forming speed should be as large as possible. This can help to increase the production efficiency.
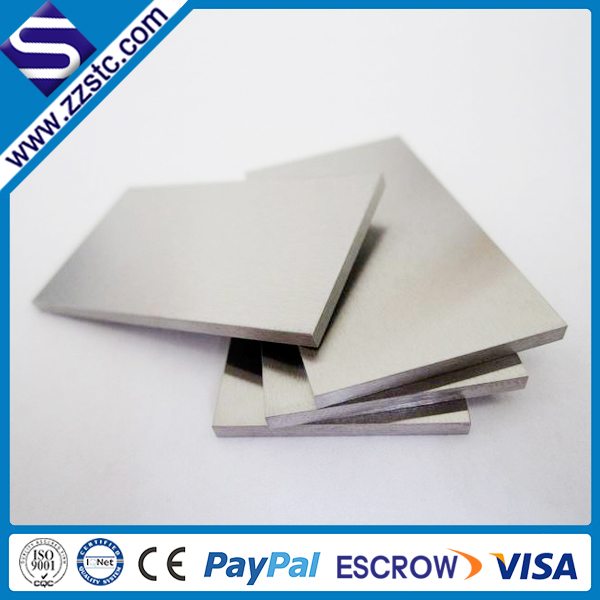
------分隔线----------------------------